Unique aspects of SCC Multi-Tiered Subcon Collaboration Process
In this blog, I want to share my experience and learnings with multi-tiered subcontracting collaboration process using my apparel client’s example. I will attempt to focus on the unique functional aspects that needs attention during any implementation of this process. Let me start with overview of the business case and the process adopted by business. Later, I will deep dive into the key building blocks and its details.
Business Case and Process adopted with SCC
One of my apparel clients in USA is sourcing garments from China’s manufacturer. A special fabric is used in manufacturing of specific silhouettes of garments. This fabric is sourced from Ethiopian (East Africa) supplier. In this case my client, was looking for drop shipment process for special fabric from Ethiopian supplier to Chinese manufacturer to save transportation time and space in their own warehouse. Chinese manufacturer was provided the visibility of the fabric order via manual spreadsheets and e-mails, so that he can plan the production and subsequent shipments accordingly.
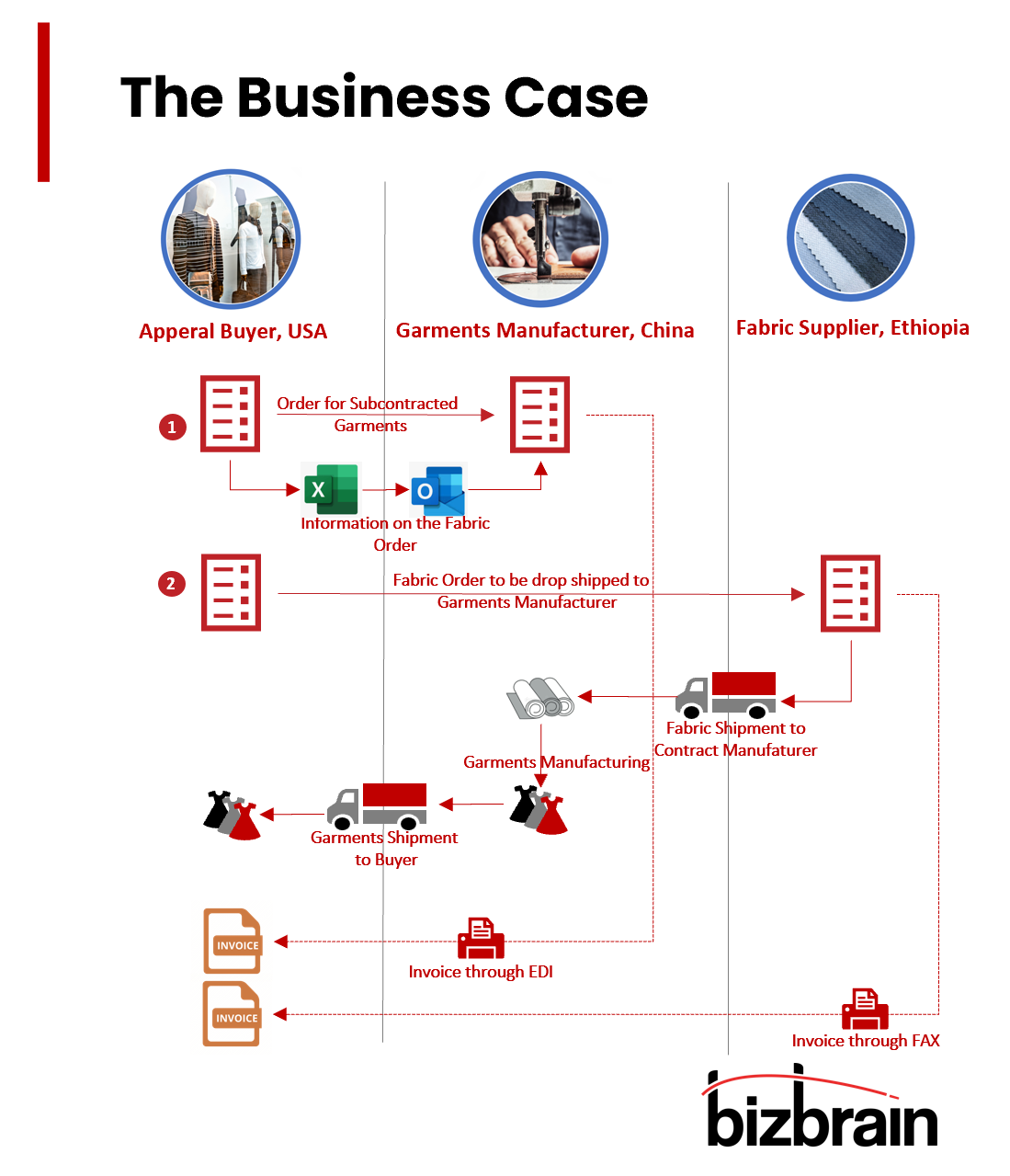
Figure 1: The business case for multi-tier subcontracting process
Let us have a quick look at the process flow for the given business scenario. Here, the flow begins with the Buyer business creating a subcontracting purchase order for garments manufacturer in China, as marked with red dot 1 in figure 1 .
There is second purchase order created in this process which is standard purchase order for fabric supplier. The important thing to note is that this order is “Drop Shipment” to garments manufacturer, marked with red dot 2 in figure 1. Fabric supplier drops Fabric at subcontract manufacturer. The shipment is done to USA buyer after manufacturing process is completed. Invoices from both parties flow to buyer through Fax or legacy EDI technology.
With SAP SCC implementation, the as-is business case shown in figure 1 got transformed into the process flow as depicted in figure 2 where the all the entities like buyer, subcontractors and suppliers were closely integrated to gain visibility and collaboration on every order confirmation, advanced ship notices, shipments, and receipt processes. This collaboration eliminated the manual work through e-mails, spreadsheets, faxes, and legacy EDI.
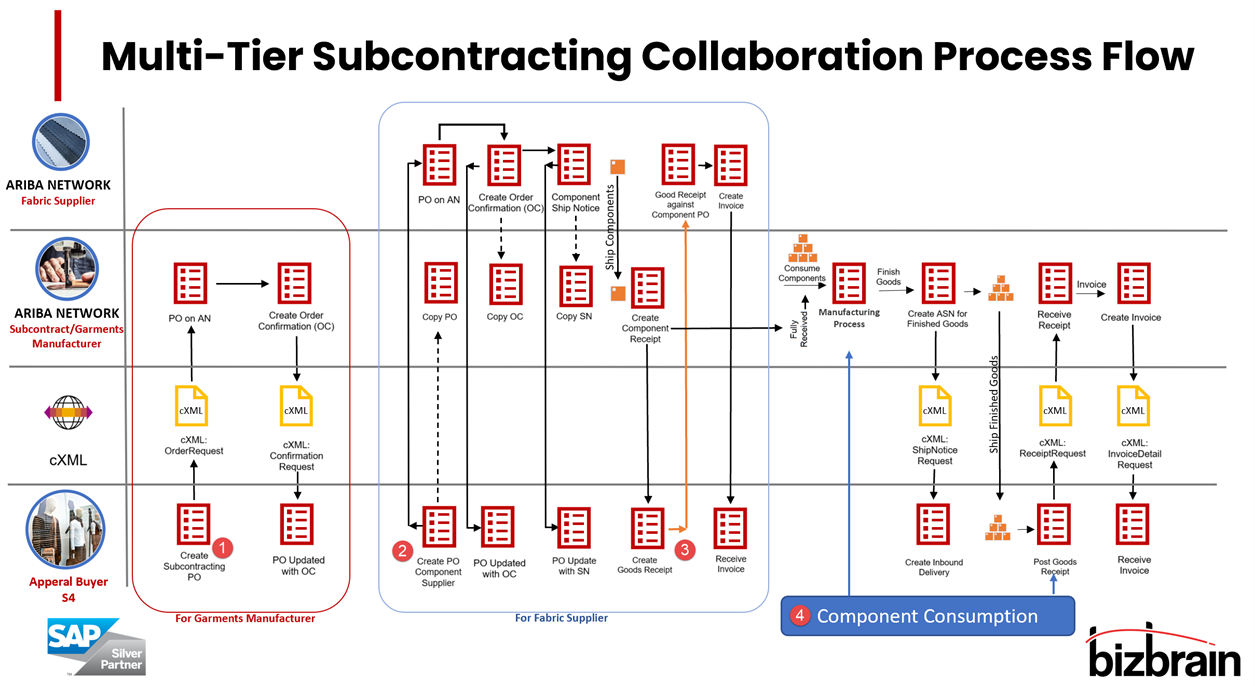
Figure 2: SAP SCC Process flow for subcontracting collaboration
I plan to focus only on unique building blocks for multi-tier subcon collaboration which are marked with four red dots in the figure 2.
- Subcontracting Purchase Order
- Standard Purchase Order with drop shipment to partner
- Components receipts (during the drop shipment) and inventory alignment
- Component Consumption reporting options
Prerequisites for the process
As our feet is wet enough with process understanding, I can now go deeper into the water. Let me first talk about the two purchase orders in the process flow.
Multi- tiered subcon collaboration needs following prerequisites from orders perspective:
a) A subcon category Info. record for a subcon material required from vendor at location and purchase org. and standard category for other materials from the various other material vendors at location.
b) BOM structure set-up and assigned to subcontracted material using T-Code CS01. The BOM needs to be assigned in the MRP 4 tab of material master data through production version.
If ECC or S4 is already implemented at client, we need to ensure that the data is maintained for Info. records and BOM and it aligns with our business requirements. Ensure that component item category is set as “L” (Stock Item), otherwise inventory will not be consumed.
Order creation for subcon collaboration
As I have mentioned in the section above, that this process requires two types of purchase orders to be created.
- One for the subcontract manufacturer, its garments manufacturer in our case, this would be subcontracting purchase order
- Second for the supplier, its fabric supplier in our case. This would be standard purchase order with drop shipment supplier
The table below defines the difference between the various parameters maintained in purchase orders.
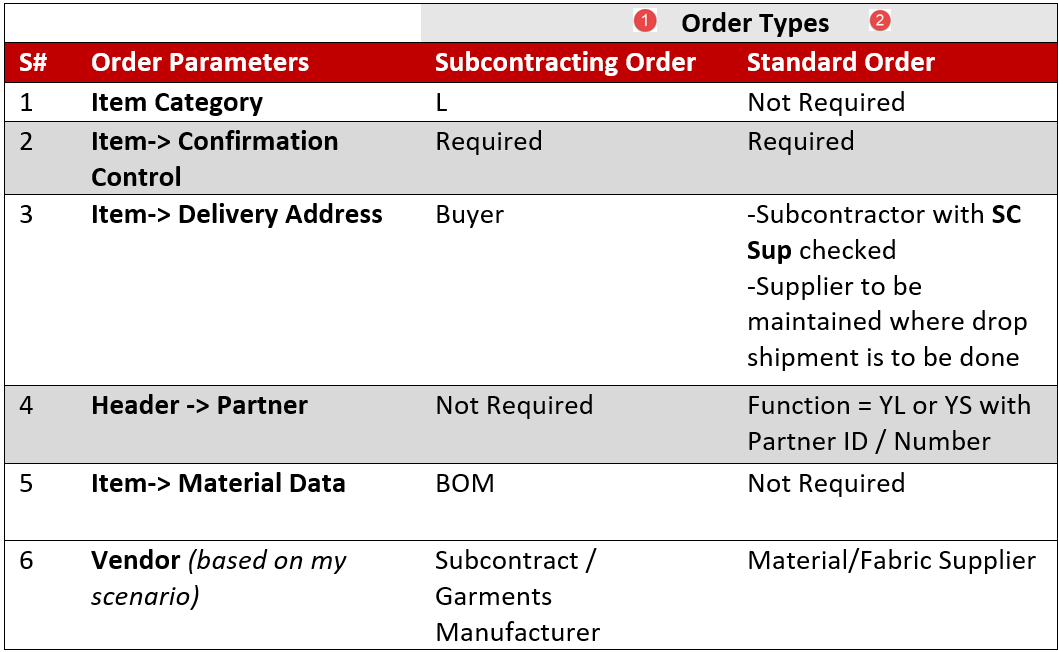
Figure 3 shows an example of a Subcontracting PO where I want to show you where and how does these parameters exist. Please correlate the bullet numbers with red dots in figure 3.
The order for SKU “Ball Gown RED XS” has
1. Item Category= “L”
2. Conf. Control = “Confirmation”
3. Delivery Address is buyer’s address i.e., Storage location 171A
4. Not Required based on table above
5. In Item -> Master -> Component tab is active once you click it, it shows components list.
6. Vendor in this order must be subcontract manufacturer
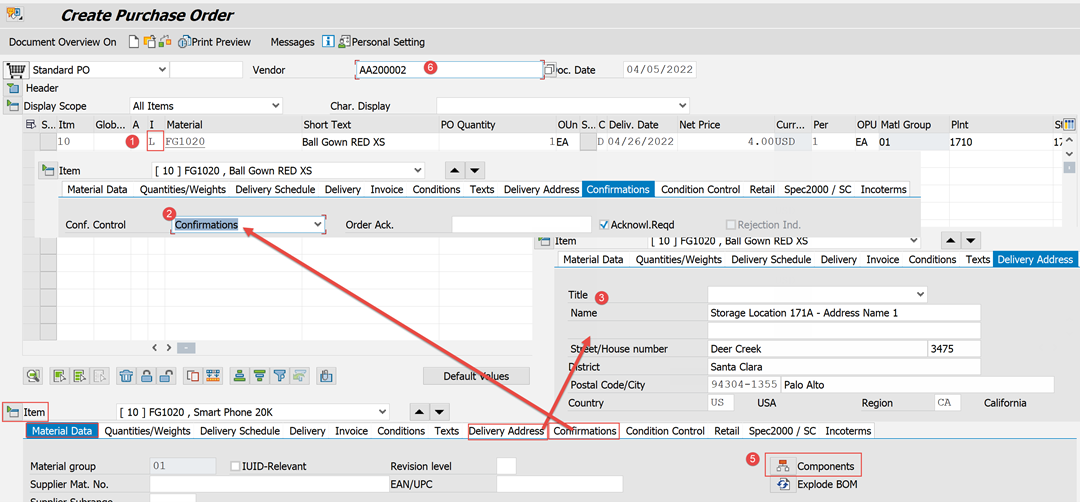
Figure 3: Example of Subcon Purchase Order
Figure 4 shows the example of a Standard PO with Drop shipment case, please use same correlation as above
The order for Fabric material has
1. Item Category= BLANK
2. Conf. Control = “Confirmation”
3. Delivery Address is Contract Manufacturer address i.e., AA200002 (same as used in Subcon PO in example above)
4. Partners maintained as “YS” and value is AA200002 where we intend to drop ship and copy all the communication from fabric supplier
5. In Item-> Master-> Component not required
6. Vendor in this order must be component supplier, for me its Fabric Supplier
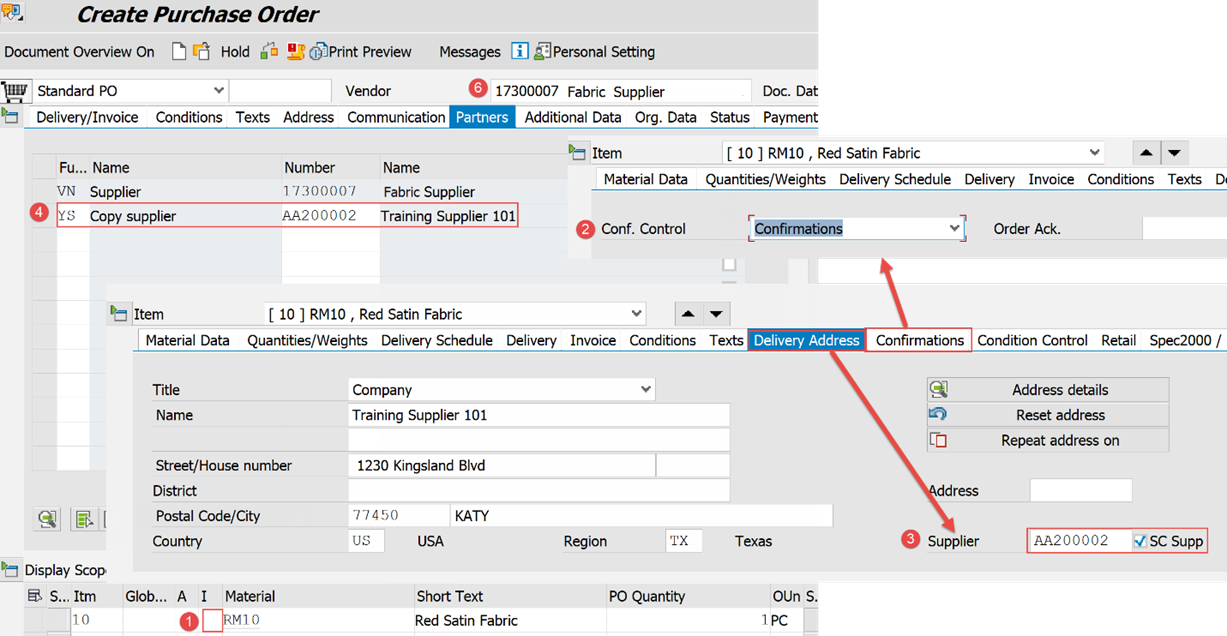
Figure 4: Example PO for Drop Shipment and sharing information with subcontract manufacturer
Multi-tiered subcon process component receipt process and inventory alignment
Order confirmation, Order confirmation deviation approvals, Handling units, Batch and other PO related processes will work in equivalent manner in this process also.
The uniqueness comes when component supplier sends ship notice to buyer, and it gets copied to subcontract/garments manufacturer i.e., when drop shipment happens at subcontract/garments manufacturer. He performs component receipt process and material document is communicated to buyer system. It is depicted in figure 2 with red dot 3 . This must be followed by alignment of the inventory between buyer and subcontract manufacturer by executing product activity message for the material, plan, and subcontractor (Program: ARBCIG_PRODUCT_ACTIVITY).
Note that :
– Relevant movement types must be configured according to CIG configuration document4
– The output type WE03 must be configured
We can visualize this document in ARIBA supplier portal by navigating to “Fulfillment” -> “Extended Collaboration” -> “Multi-Tier Shipment.”
Click on the ASN used to “Create Component Receipt” step of the process flow in figure 2.
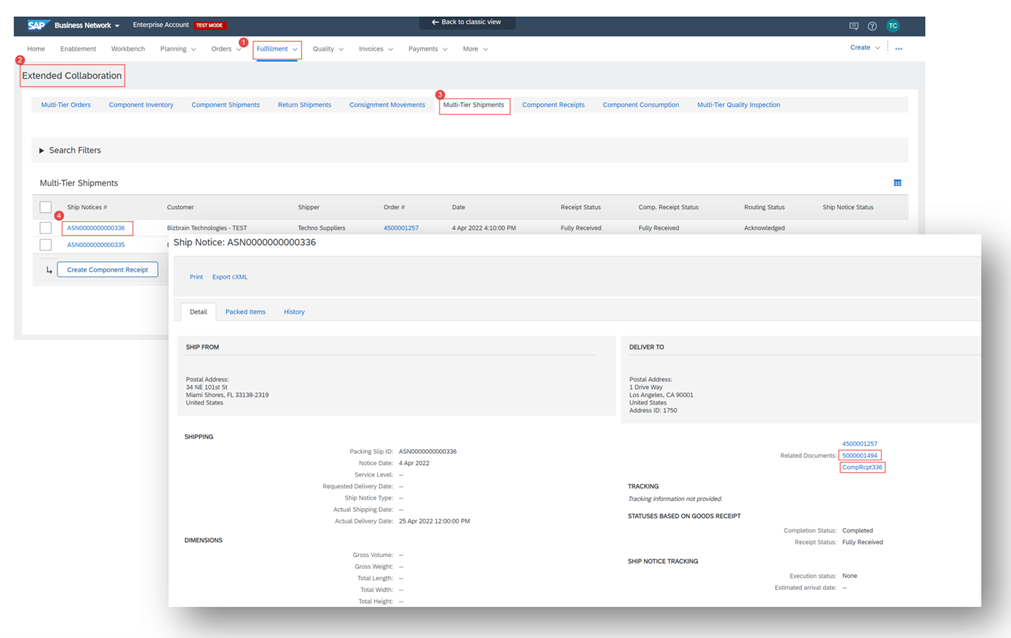
Figure 5: Supplier portal screen to see ASN receipt (POD) in multi-tiered subcon process
The ASN shown in figure 5, shows all the related documents like delivery note and material document.
Component consumption reporting process
After component receipt is completed in the previous step, the subcontract manufacturer can consume the components. There are two options to report the consumption to buyer as mentioned below:
1. Real-time inventory consumption message: A real-time component consumption message informs the buyer of consumption of components at any phase of the production cycle.
To activate this feature, activate the LOG_MM_OM_1 business function.
2. Backflush component consumption message: A backflush component consumption
message is a type of ship notice request that informs the buyer of the completion of finished goods from subcontracting components. Unlike real-time component consumption reporting, backflush reporting is done only once, at the end of the production process.
To opt for this feature, we need to configure output type “DSNO” under the application V2 (Shipping) as defined in standard configuration document.
Customers prefer backflush option, from my experience
Conclusion
As a conclusive remarks, if the fundamental building blocks for PO collaboration, order confirmation deviations, handling units, batch management are accomplished well, and the aforesaid four key building blocks and I re-iterate them below, for multi-tiered subcon process, if set correctly,
1. Subcon purchase order for subcontractor
2. Drop ship purchase order for material/component supplier
3. Goods receipt setup for Subcontractor and its flow back to material/component supplier
4. Component consumption option (Real-time/Backflush) setup
then this collaboration enables buyers, subcontract manufacturers, and materials/component suppliers even the logistics partners or co-packers to have complete visibility and control on the various goods movements, documents flow across the complex supply networks. This SCC collaboration offers multifaceted advantages to all partners. An overall win-win proposition for all business partners in ecosystem.
REFERENCES
- Defining output control for ship notice request and return delivery: https://help.sap.com/viewer/32ba8b3dbca645e9b8b7b3e84d61e3db/2202/en-US/13219eb6e3af4c369fe323de3654ad6a.html
- Configure the real-time component consumption for subcontracting purchase orders: https://help.sap.com/viewer/32ba8b3dbca645e9b8b7b3e84d61e3db/2202/en-US/b37fa70ac9eb4da38e0a28671f1354ad.html
- Maintain parameters for component consumption request:https://help.sap.com/viewer/32ba8b3dbca645e9b8b7b3e84d61e3db/2202/en-US/ec000fb8ee64485ab832a28dce77c2a0.html
- Maintain Movement types: https://help.sap.com/viewer/32ba8b3dbca645e9b8b7b3e84d61e3db/2202/en-US/9989811854884ecbab9462bf4fdc9b76.html
- SAP ARIBA Supply Chain Collaboration Product documentation:https://help.sap.com/viewer/product/ARIBA_SCC/cloud/en-US?task=discover_task
Author: Rahul Mohnot - Bizbrain Technologies
Similar Blogs
Handling Unit in Ariba SCC
Summary of the important S/4 settings by Bizbrain’s Solution Architect, Gaurab Pantu
Read moreThe Next Level of Planning Processes
How SAP Integrated Business Planning Improves Logistics Planning
Read moreHow to achieve supplier collaboration in an optimized way
When I started writing this article, I decided not to use the word “COVID.” Everything we have read and experienced for the last eighteen...
Read more